Supply Chain
BOOSTING TRADE PROFITABILITY REQUIRE COST EFFECTIVE SUPPLY CHAIN
Overview
OIP Education & Professional Services kft, (“OIP Services”), Budapest is a company registered under the laws of Hungary. One of the objectives of the company is to provide services for supply chain and contract and claims management to process industry projects at economical rates. When Clients so require, OIP Services can provide general terms and conditions for procurement of materials and construction subcontracts.
The OIP Services for procurement of materials will include market research specific to the project, preparation of procurement strategy and procurement plan, preparation of vendors’ list, preparation of material requisition, management of bids and bid evaluation and placement of purchase orders. OIP Services can also provide post order management of activities such as approval and control of drawings and documents, expediting and inspection, logistics and purchase order close-out. Purchase order close-out will cover completion of scope of work-material and documentation and financials-payments, liquidated damages, and release of bank guarantees.
OIP Services for construction subcontract consists of preparation of bid document, subcontractors’ pre-qualification, securing responsive bids, bid evaluation and award of subcontract after requisite approval. On-site services will cover subcontract management activities such as subcontractors’ invoice certification and processing of extra work requests from subcontractors. Where required, the OIP Services can provide procurement of material and warehouse management at site.
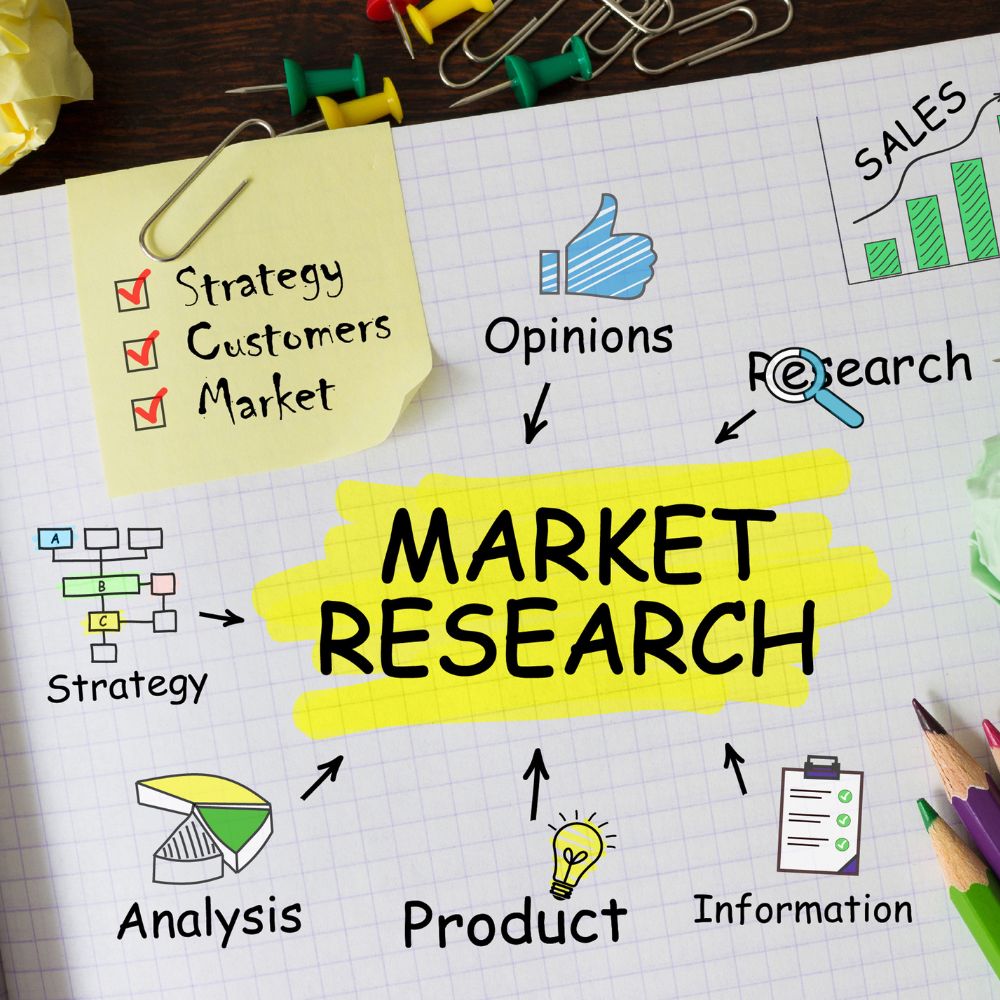
Market Research
The market research is a process of collection and analysis data on supply chain which can support logical decision on purchase activities. It can provide valuable information on suppliers and the current operating environment. In relation to supply of material and construction subcontract, every project has its unique supply chain requirements and therefore must be planned accordingly. A systematic market research can provide critical information such as SWOT analysis of suppliers, raw material availability, pricing, and suppliers recent performance.
To commence market research, OIP Services will assess requirement of supplies for the project and use this data for preparation of preliminary vendors’ list based on the experience of the Client and OIP Services. After compilation of preliminary vendors’ list, OIP Services will prepare a questionnaire to missing information with supporting documents from suppliers. This process will help to fill the gap in the information already available. The questionnaire will seek information related to:
• Company data
• Organisational set-up
• Financials for past 3 years including bank references.
• Information on products on offer for the project
• Manufacturing facilities available
• Quality control systems
• Recent experience on similar supplies made.
After evaluation of response, the necessity of on-site verification will be defined e.g. video conferencing with supplier and visit to supplier premises.OIP Services can visit important suppliers and construction subcontractors to assess the responses.
After completion of market research, OIP Services shall prepare a final vendor list using following criteriato obtain Client approval:
• Vendors list as provide by Licensors for items to be purchased from Licensor qualified vendors.
• Materials for which vendors are Nominated or Novated.
• Long lead items having a delivery period more than 12 months.
• Equipment and package plant, and construction subcontractors costing more than EUR 250,000.
• Bulk material requisitions which may cost a minimum of EUR 250,000.
• All other items
Procurement
Before commencement of procurement of materials and award of construction subcontracts, OIP Services will prepare a procurement plan which will define each major activity, consistent with Client operating procedure. This document will define the procurement process and the functions of Procurement Team with following objectives:
• Obtain economic prices based on terms and conditions for the project.
• Obtain deliveries consistent with project schedule.
• Purchases consistent with modularisation or pre-fabrication strategy.
• Guarantees consistent with project requirements.
• Compliance with project Risk Management Plan.
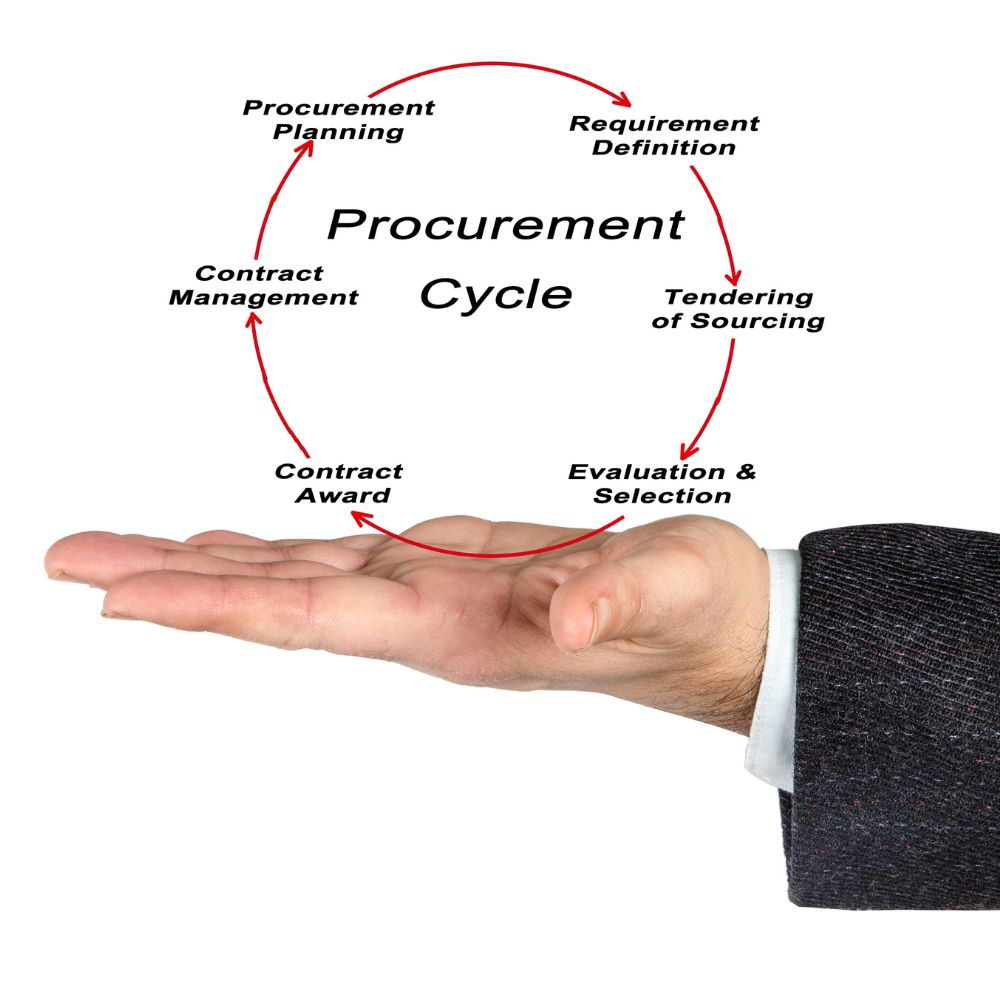
Procurement plan prepared by OIP Services for materials and construction subcontract will provide for following steps in details:
General Terms and Condition of Purchase (GTC): The standard document available with the Client shall be used after adapting it for the specific project. Similarly, other standard commercial documents such as bank guarantee forms, site service conditions etc. will be adapted for bidding.
Approval of vendors list: This shall be finalised based on the market research conducted and shall be used for all activities after approval of the Client. In case any addition or modificationsare required during the execution phase, the prequalification procedure in vogue will be employed.
Schedule of key milestones: This shall include date of release Request for Quotation (RFQ), bid submission schedule, time permitted for bid evaluation and award. The schedule shall be updated progressively.
Sourcing strategy: During bid evaluation cost of materials, spare parts and construction shall be included as delivered to site. Where the vendor is required to demonstrate performance at site, the guarantees shall be part of evaluation.
Request for Quotation (RFQ): The engineering department of the Client shall provide the Material Requisition (MR) which shall be used by the Procurement Team to prepare RFQ.
Submission of bids: RFQ shall provide the submission procedure and date for submission of bids. The bidders may be asked to submit bids in two parts, in separate envelopes- Part 1: Technical and unpricedcommercial bid and Part 2: Priced bid.
Technical bid evaluation (TBE): Bid received shall be handed over to engineering department of the Client with schedule for its completion. Engineering department shall be assisted by Procurement Team in seeking clarification from bidders and where required, Procurement Team shall arrange for a meeting with the bidders. After TBE is approved by Client, the same shall be used by Procurement Team for further evaluation. Parallel to TBE, Procurement Team shall prepare unpriced commercial bid evaluation and align the bid to suit the procurement strategy.
Commercial bid evaluation (CBE): After approval of TBE and unpriced commercial bid evaluation, all bidders will be asked to align the prices in accordance with agreement reached during TBE phase. The price comparison shall include basic scope of work, optional items, special tools, spare parts, construction costs, adjustment of cost for items not included by bidder(s) and payment terms. CBE when completed shall be submitted to the Client for approval.
Placement of Purchase Order (PO): After approval of award, engineering department shall update the MR which shall be used by Procurement Team for placement of purchase order/construction subcontract. Procurement Team shall obtain vendor’s acceptance.
Tools for procurement management: OIP Services shall use procurement tools as provided by the Client.
Procurement activities from site: In general, efforts will be made to avoid procurement of materials and construction contracts from site. In exceptional cases, Subcontract Administrator shall be made responsible for this activity.
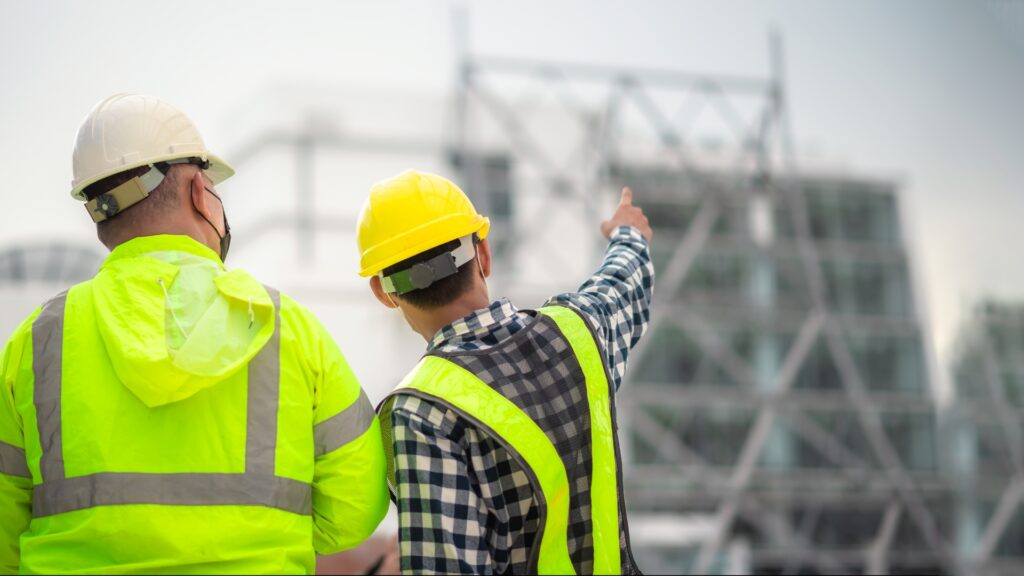
Expediting & Inspection
Kick off meeting (KOM): Within 4 weeks of purchase order for materials, Procurement Team will arrange a KOM with vendors of major/critical items with the Project Team-physical or through video conferencing depending upon the importance. Agenda for the meeting will include all aspects such as purchase order acceptance, commercial clarifications, communication procedure, verificationsand clarification of technical documents, document approval procedure, expediting plan, quality control and inspection procedure and inspection HOLD points. Purchase Team shall prepare minutes of meeting (MOM) and obtain signatures of team leaders present during KOM.
Expediting
Procurement Team shall be responsible for expediting of materials based on defined schedule. The aim of expediting includes timely document approval, status reporting on purchase order, on-time delivery and delivery of materials and final documentation in accordance the scope of purchase order. Expediting enables appropriate remedial action with vendors experiencing slippage on the schedule. Expediting will enable appropriate remedial action with vendors, if required with support of Client senior personnel. Expediting reports can form basis for control of vendor invoices for progress payments. Expediting plan will be based on following principle:
- Level 1: Low value and low priority purchase orders will be expedited through telephone.
- Level 2: Purchase orders having medium importance will be expedited through telephone and where required shall be expedited trough visit.
- Level 3: High value and high importance purchase order will be expedited through visits to the shop.
Document control
Since approval of drawings and documents is critical to the timely execution of the project, they will be expedited to ensure timely submission by vendor. After receipt of documentation, the Procurement Team will log the receipt in Document Control Matrix and make distribution for approval to the Client engineering disciplines for approval. The expeditor will track the drawings and documents internally on real time basis. The Document Control Matrix will be used to identify each of the item on purchase order and corresponding document submission requirement. Monthly progress report as may be required by the Client can be generated using the Document Control Matrix. After the drawings and documents have been reviewed/commented by the engineering, these will be transmitted to the vendor as appropriate. The process will be repeated until final approval of drawing and documents. Document Control Matrix shall be used to ensure final submission of documents on completion of purchase order.
Inspection
Project Team will coordinate all inspection requirement with Client inspection team. To clearly define inspection requirement and HOLD points, an agreement will be made during the first contact after placement of purchase order. This contact will also be used to define the inspection of sub-orders. If required, the Procurement Team will coordinate Third Party and NoBo Inspections as required for specific materials in the country of origin. In general, all material shall be identified for inspection in following categories:
- Category 1: Material to be approved based on test certificates without visit to the shop.
- Category 2: Material requiring sample checks or piece-by piece inspection-either visual or by physical testing.
- Category 3: Stagewise and final inspection during manufacturing with/without HOLD points.
- Category 4: Pre-despatch inspection for packing either through inspector or through expeditor.
Logistics
Purchase Team shall take responsibility for forwarding and transportation of materials from the source of supply to the project site. For items which require specific care during transportation, vendor’s recommendation will be taken into consideration. The Procurement Team shall ensure that:
- Inspecting of packing, marking, and loading before despatch from works.
- Plan for freight forwarding, customs clearance and onward delivery to site.
- Identify and manage transporter for over-sizedconsignments and items which require extreme care to avoid damage to materials and public property.
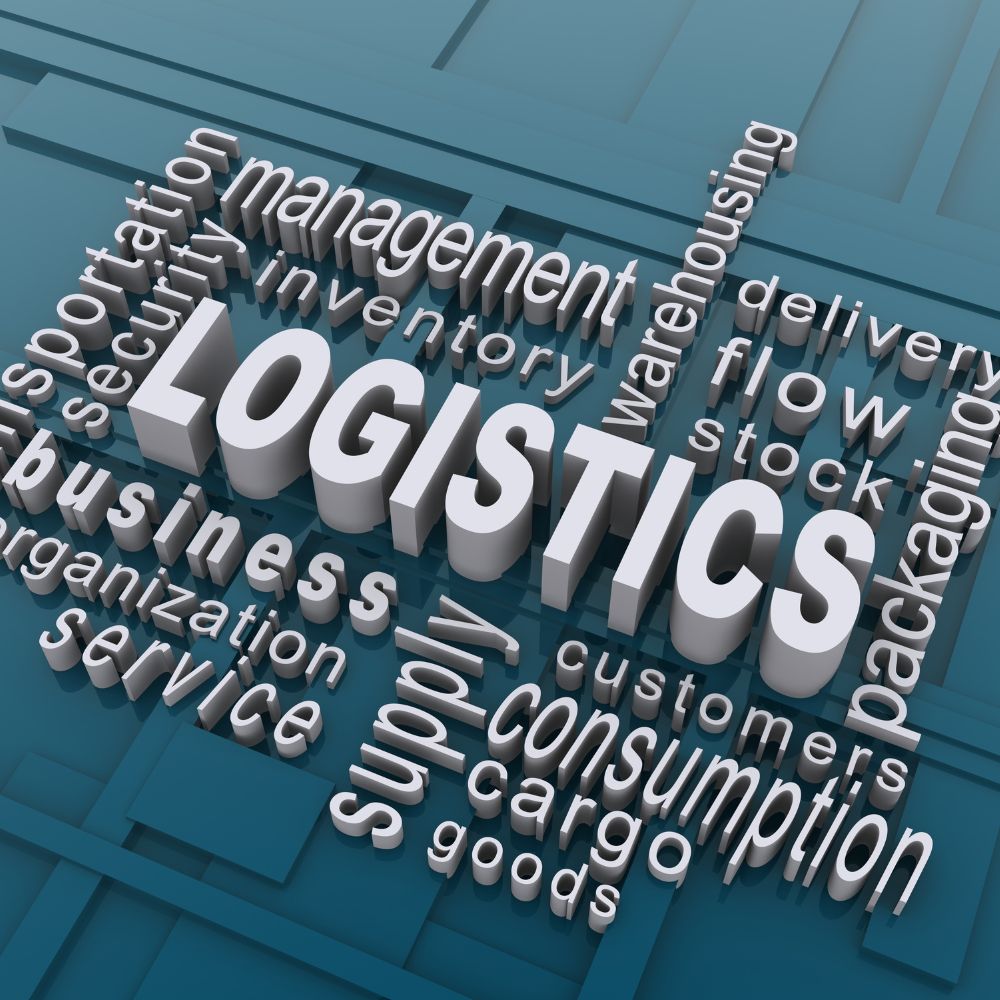
For last 50 years all Governments have been controlling human
Construction of process plants (“Project”) extend over long period of
For construction of process plants (“Project”), preferred mode of execution
During the planning phase of a chemical process plant (“Project”)
A contract, by definition, is a commitment between two parties,